How can I ensure compatibility between my battery charger and my forklift?
Forklift Charger Introduction
The shift towards electric-powered industrial vehicles, such as forklifts and other material handling equipment, is gaining momentum. This transition is driven by the desire to reduce carbon footprints, lower operational costs, and improve overall efficiency. However, to fully harness the benefits of electric vehicles, it is crucial to understand the intricacies of industrial battery chargers. This guide aims to provide a comprehensive overview of what you need to know about selecting the right battery charger for your electric industrial fleet.
The Importance of Choosing the Right Battery Charger
Investing in electric industrial vehicles is a significant step towards sustainable operations. However, the benefits of these vehicles can only be fully realized if you have the appropriate battery charging infrastructure in place. The right battery charger can enhance vehicle uptime, reduce maintenance costs, extend battery life, and improve overall operational efficiency. On the other hand, using the wrong charger can lead to reduced battery performance, increased downtime, and higher costs.
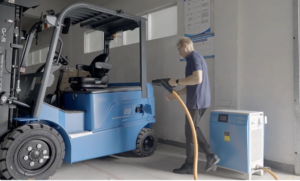
Key Factors to Consider When Selecting a Battery Charger
Before deciding on a battery charging system, several factors must be taken into account to ensure compatibility and optimal performance:
Battery Type
Different types of batteries require specific charging profiles. For example, lithium-ion batteries and lead-acid batteries have distinct charging requirements. Lithium-ion batteries are known for their fast charging capabilities and long cycle life, while lead-acid batteries require a more traditional, slower charging process and a cooldown period.
Battery Voltage
The voltage of the battery is a critical factor. Industrial batteries typically come in various voltage ratings, such as 24V, 36V, or 48V. The charger must match the battery’s voltage to ensure proper charging and avoid damage to the battery.
Charging Time
Charging time is a crucial consideration, especially in operations that require continuous use of vehicles. Fast chargers can significantly reduce downtime, making them ideal for multi-shift operations. However, they may require more robust electrical infrastructure. Conventional chargers, which take longer to charge, are more suitable for single-shift operations where vehicles can be charged overnight.
Charging Specifications
Each battery has specific charging specifications, including charge rate and maximum current. These specifications must be matched with the charger’s capabilities to ensure safe and efficient charging. Overcharging or undercharging can lead to reduced battery life and performance.
Equipment Utilization
How frequently your equipment is used will influence the type of charger you need. High-utilization operations may benefit from fast or opportunity charging systems, while lower-utilization operations can rely on conventional charging.
Electrical Infrastructure
Your existing electrical infrastructure must be capable of supporting the charger’s power requirements. Fast chargers, for example, may require higher amperage circuits and may need additional electrical upgrades.
Physical Space
The physical space available for charging equipment is another important factor. Some chargers are compact and can be easily integrated into existing facilities, while others may require dedicated charging stations or rooms.
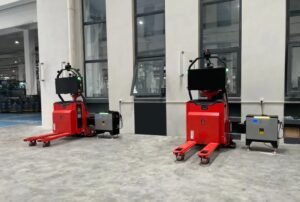
Types of Battery Charging Systems
Conventional Charging
Conventional charging involves removing the battery from the vehicle and placing it on a charger at the end of a shift. This process typically takes 8 to 10 hours and is ideal for lead-acid batteries. Lead-acid batteries also require a cooldown period of an additional 8 hours, which means you may need multiple batteries for continuous operations.
Fast Charging
Fast charging systems can charge a battery in as little as 10 to 30 minutes. These systems are ideal for lithium-ion batteries and are perfect for high-use, multi-shift operations. Fast charging requires more advanced electrical infrastructure and may need additional cooling systems to manage heat generated during the charging process.
Opportunity Charging
Opportunity charging takes advantage of short downtime periods to charge the battery. This method is particularly effective for lithium-ion batteries, which can be charged quickly and efficiently without the risk of reducing their cycle life. Opportunity charging is ideal for operations that cannot afford long downtime for charging.
Conclusion
Selecting the right battery charger for your electric industrial vehicles is essential for maximizing efficiency, reducing costs, and ensuring the longevity of your batteries. By understanding the factors that influence charging, such as battery type, voltage, charging time, and equipment utilization, you can make an informed decision that aligns with your operational needs. Whether you opt for conventional, fast, or opportunity charging, the key is to match the charger to your specific requirements.